Quality Control in India: 7 Red Flags You Shouldn’t Ignore
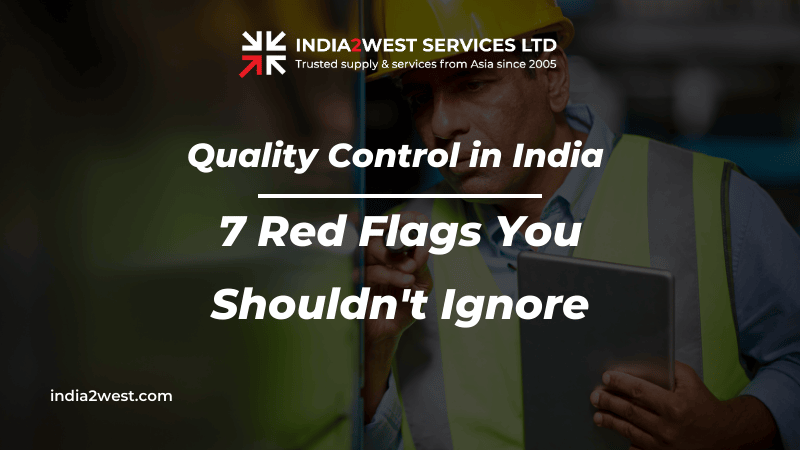
When sourcing products from India, quality control is a crucial factor that can make or break your business. India is home to a thriving manufacturing industry, but it’s essential to recognize potential pitfalls before they become costly problems. While there are many benefits to sourcing from India, a lack of rigorous quality control can lead to defects, delays, and reputation damage.
In this blog, we’ll explore 7 major red flags to watch for when dealing with quality control in India. By understanding these issues early on, you can mitigate risks and ensure your products meet global standards.
1. Lack of Clear Quality Standards
One of the first signs of potential trouble is when a manufacturer doesn’t have well-defined, transparent quality standards. Without clear quality benchmarks in place, you may face issues like inconsistent product quality, delays, or miscommunication regarding expectations.
Before entering into a partnership, ensure that your supplier in India has a documented quality control process that is aligned with international standards, such as ISO or Six Sigma. This documentation should outline the procedures, tools, and protocols used to assess product quality at every stage of production.
Establishing these standards from the beginning will help protect your business from defects and delays, ensuring that the manufacturer can consistently deliver quality products.
2. Poor Communication and Transparency
Another critical issue is poor communication throughout the production and quality control process. If your Indian supplier is not responsive or transparent about the status of your order, it can indicate deeper issues with quality control.
Effective communication is key to ensuring that your expectations are met and any quality concerns are addressed promptly. This includes regular updates, sharing of production timelines, and openness about any potential issues that arise during manufacturing. Suppliers should be proactive in keeping you informed about progress and challenges so that you can address problems before they escalate.
If communication becomes a struggle or your supplier is hesitant to discuss potential quality issues, consider this a major red flag and reassess your partnership.
3. Lack of Proper Certifications and Compliance
Manufacturers in India, especially those involved in electronics or food production, should comply with industry-specific certifications, such as ISO, CE, or other relevant standards. If a manufacturer cannot provide proof of these certifications or insists they are not necessary, it could indicate non-compliance with industry regulations, leading to quality issues.
Always request verification of any relevant certifications and check for compliance with international standards. If the manufacturer refuses or cannot provide this information, it could mean they are cutting corners.
4. Lack of Experienced Quality Control Personnel
Quality control requires skilled professionals who can detect and correct defects early in the production process. If your supplier in India lacks experienced quality control personnel or is relying on untrained staff, your products may not meet your required standards.
It’s crucial to ensure that the manufacturer has a qualified team in place to oversee all aspects of quality control. Look for companies that have certified quality control managers, engineers, and inspectors who are trained to identify defects, perform detailed inspections, and make necessary adjustments to the production process.
When your manufacturer’s quality control team is well-trained and experienced, you can feel confident that they are actively working to maintain product quality at every stage.
5. Unclear or Incomplete Contracts
A contract serves as a safeguard for both parties, clearly outlining the expectations, timelines, pricing, and quality standards. If your manufacturer avoids providing a detailed contract or offers an incomplete one, it could suggest they are not fully invested in a professional relationship.
A vague or incomplete contract increases the risk of misunderstandings, which may ultimately result in product quality issues. Ensure that all terms are clearly outlined and agreed upon, with specific provisions for quality control, delivery schedules, and dispute resolution.
6. Inconsistent or Poor Inspection Reports
In India, some manufacturers may not conduct thorough or regular inspections, or they may provide subpar inspection reports. This can be a serious red flag, as it suggests that quality control is not a priority.
Reliable manufacturers should provide comprehensive inspection reports at key stages of production, including pre-production, during production, and before shipment. These reports should cover everything from raw material quality to final product assembly and packaging. If a manufacturer fails to provide clear, consistent inspection reports, it’s a warning sign that they may not be adequately overseeing their quality control processes.
7. Overlooking Post-Production Quality Checks
While pre-production and in-process inspections are essential, post-production checks are just as important. Many suppliers in India may rush through the post-production phase, either due to pressure to meet deadlines or a lack of resources. This oversight can lead to a number of issues, from defective products to incorrect labeling and packaging.
Ensure that your Indian manufacturer performs a thorough final inspection before shipment, which should include:
- Functionality testing
- Visual inspection for defects
- Packaging and labeling checks
- Compliance verification with your specifications
A solid post-production quality check process guarantees that your products will be ready for the market, minimizing returns and customer complaints.
Drive Your Success To New Heights With India 2 West
When sourcing from India, quality control is not something you should overlook. By recognizing and addressing these five red flags early in your partnership, you can avoid costly mistakes and ensure that your products meet the highest standards.
To avoid these pitfalls, it’s important to partner with a supplier who prioritizes quality, maintains transparency, and has the right team and processes in place. This will ensure that your products arrive on time, within budget, and free of defects, helping you build a reputation for quality with your customers.
If you need help navigating quality control in India or are looking for reliable manufacturers who prioritize quality, get in touch with us today. Our team is here to guide you through every step of the sourcing process. We’ll help ensure your products meet global standards and are delivered on time.